3 Ways Manufacturers Can Leverage Digital Feedback Loops
- Brad Zorn
- Sep 16, 2022
- 5 min read
Updated: Oct 4, 2022
Feedback loops are simple to understand: measure conditions as you produce something and use that information to improve production. Around it goes – a constant cycle of monitoring and improvement.
Feedback is information about what happens as a result of what you produce, service, or monitor. You can use that information to adapt your productions and methods, creating what is called a feedback loop. A digital feedback loop uses digital technology at some stage of the feedback loop.
In manufacturing, feedback loops are best when leveraging digital technology to collect and share feedback data, which have huge potential when collected through equipment with sensors.
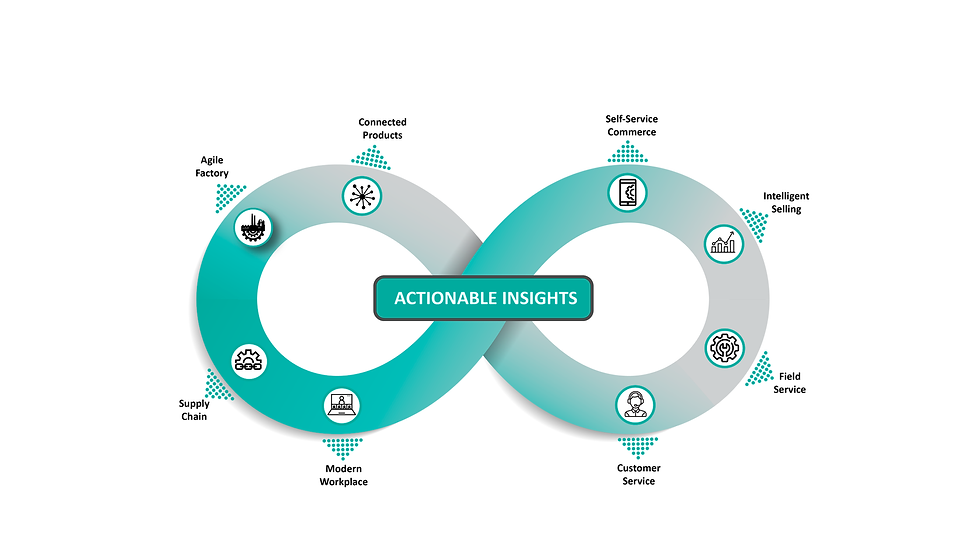
We're focused on manufacturers, and I love thinking about digital feedback loops as they relate to the Intelligent Enterprise. Manufacturers are facing volatility, uncertainty, complexity, and growing customer expectations like never before. This is why companies need to make the most of their investments in cloud, mobility, analytics, and artificial intelligence by leveraging their data to provide actionable insights that empower their teams to make proactive, real-time decisions. Data from every facet of your enterprise is constantly connected, feeding insights that lead to better decisions that impact your bottom line and customer loyalty.
Industry 4.0 is proven to optimize performance, improve efficiencies, reduce costs, and deliver better value to customers.
The first trick is capturing data with context for an event. Capturing information without context has some value, such as what was the tonnage of the last press stroke but is enhanced with context like what item or material was part of that press stroke. It’s also iterative – for example once we know both the machine conditions and material, it might now be critical to understand what batch of that material was being used, or even detail about the batch quality characteristics.
Once we have the right data set, how do we take this and make better, proactive decisions, and learn from it? There are many industry use cases on using feedback loops to increase uptime, reduce cycle time, and improve quality… but how do we scale feedback loops to extend to the broader relationship between a manufacturing company and its customers, improve employee performance, and impact supply chain decisions?
Here are a few examples of feedback loops that can be used across your enterprise.
Don’t Scrap the Data
In this clip from a recent Agile Factory Learning series, which you can stream on demand here, Kennametal Plant Manager Frank Constantine discusses how machine data is helping them solve problems they never could before. He discusses how equipment measurements of tonnage helped them solve a sizing issue down later in the production. They resolved the issue for a customer before it ever got to them, improved their own equipment and supply management, as well as the performance of their operator – all with data they never could have found before their Connected Factory modernization.
Supply Chain Disruptions and Changes
You can use digital feedback loops to inform decisions beyond the factory floor. It’s a fantastic use of the data and it reaches beyond those walls, just as the products you create do for your customers.
For example, let’s consider a customer placing an order for a make-to-order item that they’ve ordered from you many times before. This sales order is entered, a supply plan generated, and a production schedule created. The demand goes to the shop floor, and it sits there for 3 days while a critical piece of tooling is out for reconditioning. The process engineer used insights from the tool’s performance and durability tracking to proactively send that tooling for reconditioning before it risked failure. Sound like a plausible situation in your company? In isolation, these things sound like solid industry practices leveraging what I4.0 unlocks. Without feedback looping from the tooling system to the supply/demand systems, your customer just gets the order three days late, or calls when it hasn’t arrived, and you now have another expedite on your shop floor. Further, the reaction is often to “buffer” routing steps to accommodate for all the unknowns like this on the shop floor – I’ve seen examples in the past of a product that takes just a few days to manufacture have systemic lead times of 15 days. Imagine a feedback loop cutting your lead time to a fraction of its current value; what would you give for that level of agility?
It’s important to think about how any factory insights can help to reorganize production schedules, notify customers of manufacturing progress, forecast late orders, and impact constraint-based scheduling. In the lead time example with buffers built into the routing, we can use data to determine how much of that is dwell time and use IoT and process data to focus on improvement to reduce cycle time variation. Maybe the standard cost associated with the routing isn’t as accurate as we thought it was, either… but that’s probably more worthy of a financial blog than a Smart Factory one!
Customer Service
Customer Service is ripe with opportunity for your data to improve loyalty, offerings, and experiences, while also offering insights that can be used to improve your product design.
Data allows you to become proactive. Your teams can service equipment before it has issues, upgrade equipment that could be performing better, or even replace outdated equipment that has not been meeting standards for a proven period.
You can also use that same equipment information to inform the design of your products by providing feedback on material science to engineering teams on the manufacturability of their designs. You can also see how well your field service repairs and replacements are working.
In this clip, Brad Kerr, a Principal Program Manager for Microsoft, discusses Project Bonsai, a program built around speeding the creation of AI-powered automation and how it helps improve product quality and efficiency while reducing downtime. He explains a couple different examples of how a digital feedback loop informs AI to improve a favorite cheesy snack of kids (and kids at heart) – Cheetos. The AI is using feedback from machines to make autonomous decisions to change outputs that improve throughput and quality. He also discusses how a canning manufacturer is using an AI supervisory control across an entire production line – the creation of aluminum cans to finished product. They trained the AI on the entire process using digital feedback loops to improve production.
For more on this and other topics, I invite you to stream a series of events hosted by Microsoft called The Agile Factory: Industry 4.0 Learning Series for Manufacturers. I joined some of the best minds in manufacturing to discuss best practices for bringing your Agile Factories and digital transformations to life. You can stream the entire four-part video series by clicking here.
Comments