
In Their Own Words
"Equipment is the heart of my customer’s business – and my goal is to make sure they’re getting maximum uptime while running at peak efficiency. As an invaluable asset, equipment needs to provide all available intelligence through sensors and connectivity to avoid sub-optimal performance, failures, and unnecessary maintenance.”
Daily Challenges Include
-
Complete Asset View + Asset History
-
Service Twin for Analysis
-
Predictive Maintenance
-
Machine Learning Entitlements
-
Inspection Visibility
How I'm Measured

Issues + Trends at the Component Level

Current Runtime +
Remaining Useful Life

Current Running Conditions
What I Need To Succeed
-
A way to provide my data, either through a direct cloud connection or indirect data acquisition through sensors.
-
A digital version of all parts in a centralized system to equip tech support and field techs with a 360-degree view.
​​
-
Complete history from install to maintenance at a granular level to reduce research time and lower time to resolution.
​​
-
A record of required parts and services so the tech comes prepared and resolves the issue correctly the first time.
​​
-
Regularly scheduled maintenance to prevent common issues and repair costs.
​​
-
Warranties, agreements, and entitlements

Equipment Digital Twin
Prevent equipment failures before they occur with remote monitoring and troubleshooting commands. Increase asset uptime, first time fix rates, and build a maintenance plan based on predictive insights. Customers also benefits from faster research and response times by customer service and field technicians having a 360 view of equipment details.
Complete History View
Decrease research and repair time by accessing the service history behind customer equipment by referencing past repairs, or following up on recommendations from a previous service visit.
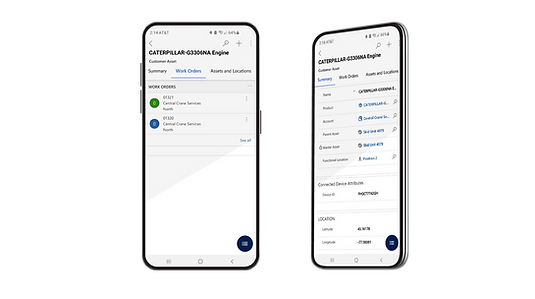
Ready to see for yourself how equipment360™ can upgrade your company's service game?